The Interphase Transport Phenomena (ITP) Laboratory is engaged in a number of activities related to the development of thermal-fluid technologies and … Read More
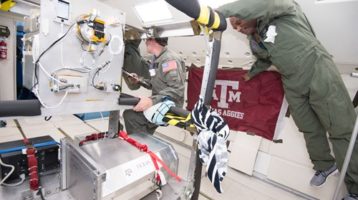
DoVR Parabolic Flight a Success
Dr. Cable Kurwitz and three Texas A&M Undergraduate Engineering students recently completed a successful flight test program … [Read More...]
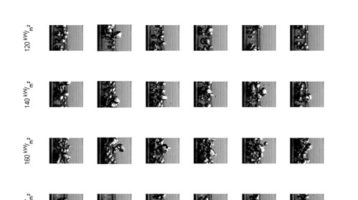
Fun with Boiling
Inferring information from video is desirable since video data is becoming more accessible due to improvements in recording and storage. Machine learning techniques are also … [Read More...]